Following the launch of the world’s first 100 percent post-consumer aluminium, Hydro CIRCAL 100R in 2024, Hydro is shifting its attention to transportation. By working within very small manufacturing clusters in the Netherlands and Belgium, the transportation emissions of this year’s design objects are reduced by 90 percent compared to last year.
The second chapter of Hydro’s Milan series continues to highlight the company’s ongoing efforts to achieve net-zero emissions by 2050, examining every level of the aluminium manufacturing process to get there.
“We choose to be present at Milan Design Week because this is where the most groundbreaking developments in materials and design, across industries, are presented. It is a fitting venue to showcase Hydro’s unique capabilities in design, manufacturing and low-emission aluminium,” says Eivind Kallevik, President and CEO of Hydro.
This year’s exhibition of examining the transportation footprint comes as a natural extension of the 2024 project. The launch of Hydro CIRCAL 100R, with its carbon footprint below 0.5 kilo CO2e per kilo aluminium, represented a major milestone for Hydro.
“When the starting point is a material with a very low-carbon footprint, this sets the standard for everything else we do,” says Kallevik.
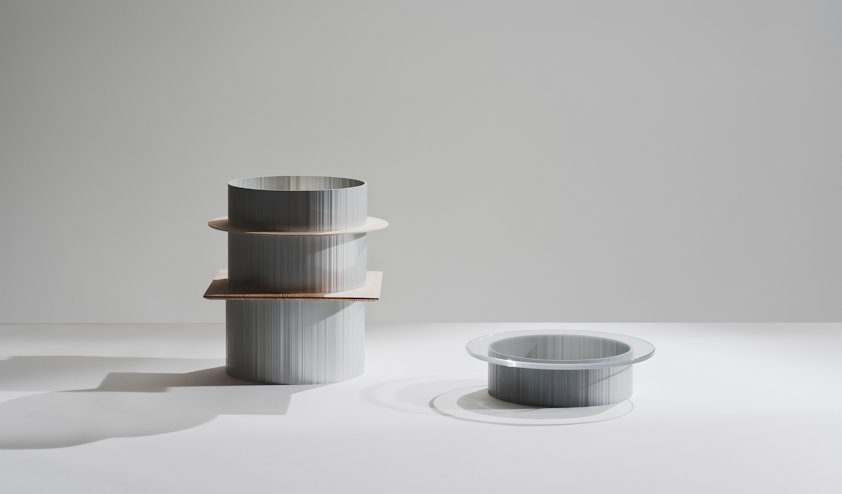
World class designers with no limitations
The R100 designers, Sabine Marcelis, Keiji Takeuchi, Cecilie Manz, Daniel Rybakken and Stefan Diez, were all unaware of the 100 kilometers production radius when designing. The designers were offered complete freedom by Hydro, with no limitations to extrusion press size, product size or product typology to make sure the project mirrors a real life use case, where customers get access to everything Hydro can offer, from design support to production processes.
The idea of containing the entire project within a very small manufacturing cluster was to reduce the carbon emissions related to transportation, while also potentially reducing lead times and increasing efficiency.
“Shortly after the 100R project was launched last year, this idea started building. Could it be possible to solve all operations from scrap collection, casting, extruding, machining and anodizing within such a small area, creating five bold new designs from 100 percent post-consumer based aluminium,” says Asle Forsbak, Marketing and Communication Director in Hydro Extrusions.
The five designers were selected for their distinct design expressions and complementary methodologies, resulting in a unique collection of mono-material aluminium products varying from home decor objects to chairs and furniture components. All products are made of Hydro CIRCAL 100R recycled aluminium.
The project officially began in November 2024, with the harvesting of 52 tonnes of locally sourced aluminium scrap from demolished greenhouses and decommissioned light poles in the Netherlands, involving a range of Hydro plants in the Benelux region.
“This is urban mining put into practice. By working with small manufacturing clusters, we can really demonstrate what we mean by radical transparency. We are sharing the transportation routes and carbon footprint data of this project to show how much transportation means for the embedded carbon footprint in a product,” says Forsbak.
Hydro CIRCAL is Hydro’s range of premium recycled aluminium, based on scrap with a previous life as a window frame, car part or other consumer products. By recycling post-consumer scrap, the material reaches a very low-carbon footprint. Hydro CIRCAL is available with 75 percent post-consumer scrap or with 100 percent post-consumer scrap in limited amounts. Hydro CIRCAL 100R comes with a carbon footprint of less than 0.5 kg CO2 per kg aluminium, 33 times lower than the global average.
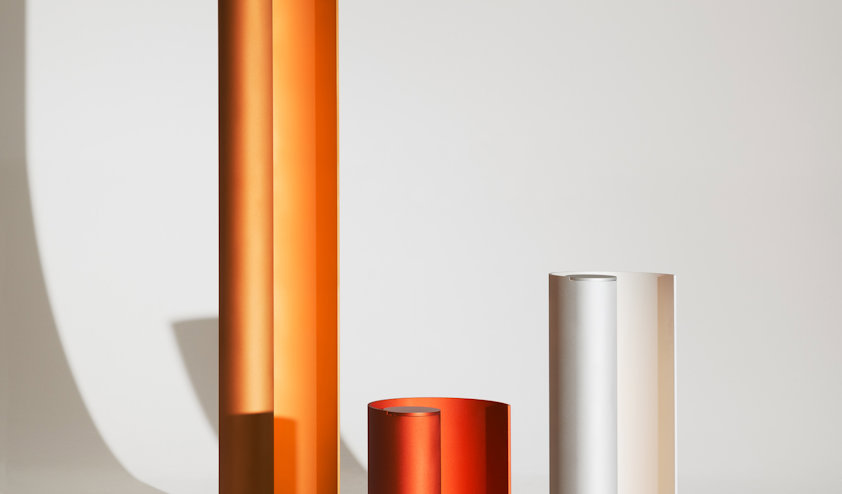
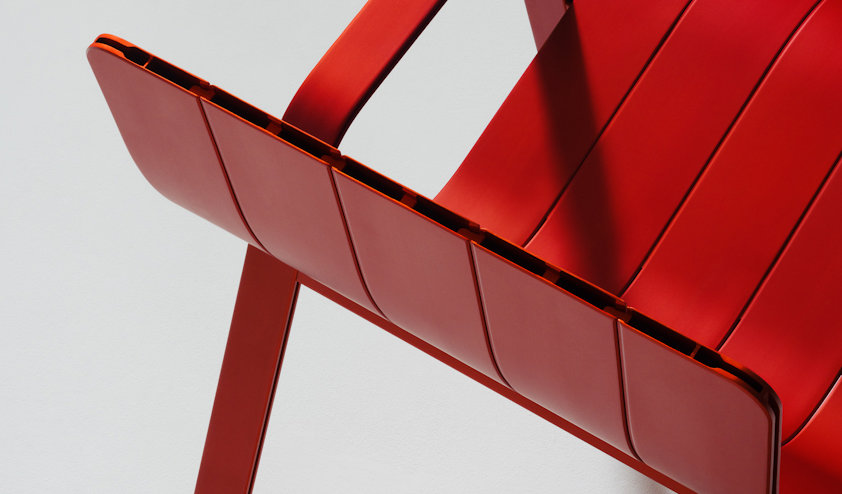
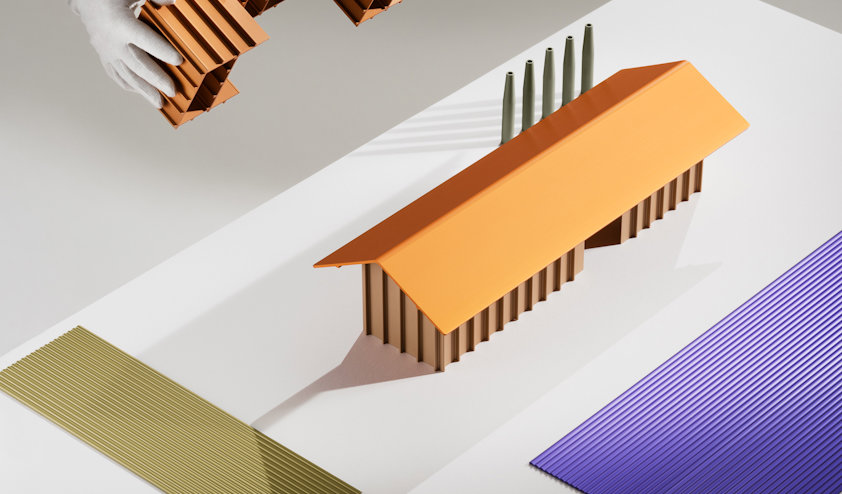
Published: April 7, 2025